R&D Engineering Co-op at Boston Scientific
I completed my first 6-month cooperative education placement at a Fortune 500 medical device company as a Research and Development (R&D) Engineer, where I worked on:
-
New Product Development
-
Novel Technologies in Electrical Circuitry and Manufacturing
-
Product Testing
-
Competitor Product Analysis
-
Prototyping and Fabrication
... and more!
I communicated with engineers and suppliers from across the globe to ensure the proper implementation of design decisions and the top-notch delivery of innovative products. Additionally, I developed test methods, performed quality inspections on product units, and trained with machinists to rapidly prototype ideas and machine parts.
My Projects at Boston Scientific
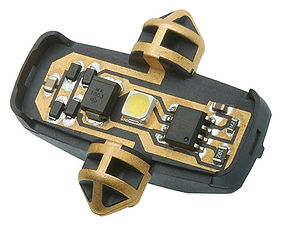
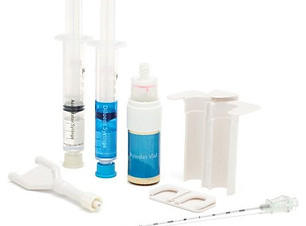

Innovative Design of an Optical Mechatronic Assembly
Test Method Development for an In-Vivo Hydrogel System
Testing, Development, and Competitor Product Analysis for a New Urological Scope
A microscopic component that could revolutionize a $1B+ market
Testing a non-Newtonian fluid used for radiation treatment
Developing a state of the art urological scope amid regulatory restrictions
Due to confidentiality, most CAD models and drawings cannot be displayed here, but can be discussed in person.
Innovative Design of an Optical Mechatronic Assembly
I invented and designed a critical mechatronic component in a medical scope, using novel 3-dimensional circuit technology and design for manufacturability and assembly (DFM, DFA) best practices, reducing its cost to be 38x cheaper than other alternatives
Skills Developed:
-
Design for LDS, MID, and 3-Dimensional Circuit Technology
-
Design for Assembly (SMT, Pick and Place)
-
Design for Plastic Injection Molding
-
Design for Micron-Scale and Microscopic Applications
-
SLA Printing
-
Engineering Tolerances
-
Global Supplier Relations
-
Internal and External Technical Communication
-
Management Presentations
Purpose:
-
Develop a cost-effective optical assembly for a medical scope containing the following components:
-
Camera, LEDs, Pressure Sensor, Resistors, Capacitors, & Coaxial Cables
-
-
Tasked with designing the component from scratch using SolidWorks and creating a complete assembly
-
Must utilize and learn the process of Laser Direct Structuring (LDS) and Molded Interconnect Device (MID) Technology
-
Analogous to 3-Dimensional Circuitry. Click here to learn more.
-
-
Communicate with global vendors to ensure the proper implementation of design decisions
Challenges:
-
Many components for little space: The space available is almost equal to a half a grain of rice
-
Technology design constraints are too large: Examples include width of conductive paths, fillet size, etc.
-
Change in design requirements: Dimensions change from vendors, change in connectivity, etc.
-
Design for Assembly (DFA): Minimize # planes components are on, use Surface Mount Technology (SMT)
-
Design for Manufacturability (DFM): 1 shot injection molding, no undercuts, etc.
-
Language barrier with global vendors
-
Technology is new
-
No experts and vendors are available
-
Design requirements keep on changing
-
Results:
-
Developed 5 major design iterations to accommodate for all the changes and different possible versions
-
Designed an LDS base that meets all design requirements
-
Vendor will manufacture units
-
Designs are under revision for patent application
-
-
Lowered cost of component to be 38x cheaper than other alternatives
-
Shared CAD internally and will be used for internal communication and with external vendors if need be
-
Presented designs internally to management and principal engineers
-
Printed an enlarged SLA Plastic version for ideation and prototyping
Lessons Learned:
-
Able to oversee a design and its development from scratch
-
Ideation and Concept Development > Manufacturing and Build
-
-
Design must be resilient to accommodate for engineering change requests
-
Gained valuable responsibility and leadership skills in a corporate business environment by heading the optical assembly design
-
Developed an understanding of the global supply chain process
Test Method Development for an In-Vivo Hydrogel System
I created test fixtures using CAD, developed test methods, and performed mechanical testing using the Instron Universal Testing System.
Skills Developed:
-
Instron Testing System and BlueHill Software
-
Technical Writing
-
Manual Milling
-
Quality Inspections
-
R&D Laboratory Testing Procedures
-
Domestic Vendor Communication
-
Ultrasound Imaging
-
Familiarity with Regulation in Medical Devices
-
Silicone Molding and Casting
Purpose:
-
Design and fabricate fixtures using CAD for various testing
-
Develop test methods to test various material properties
-
Execute test methods and report collected data
-
Perform quality inspections on units arriving from the manufacturing facility prior to testing
Challenges:
-
Long In-House Lead Times for 3D-Printing
-
Development costs should be minimized
Results:
-
Created multiple test fixtures and registered them as laboratory equipment. Fabrication techniques included 3D FDM printing, manual milling, and machining
-
Developed test methods to be validated such as vertical and horizontal injection force tests
-
Performed quality inspections on units from the manufacturing facility and reported defects
-
Looked into domestic vendors to get quotes for motors, actuators, and other parts for some apparatus
-
Trained on the Instron Testing System and performed various tests such as 3-Point Bend Tests
Lessons Learned:
-
"Keep it simple"
-
An essential engineering and design principle I got to implement over time and with each iteration
-
Now, I actively incorporate design simplicity in my engineering process
-
Testing, Development, and Competitor Product Analysis for a New Urological Scope
I analyzed competitor products and data, tested fluid flow rates in an environment simulating a human kidney, and optimized laser settings for fracturing and dusting kidney stones
Skills Developed:
-
Patents and Intellectual Property
-
R&D Laboratory Procedures and Testing Practices
-
Error Propagation and Analytical Approximation
-
Mathematical Modelling
-
Equipment Calibration
-
Communication in a Technical Environment
-
Product Investigation
-
High-Intensity Laser Procedures
-
Laser Fiber Maintenance and Repair
Purpose:
-
Evaluate and verify competitors' data and optimize it for our purposes
-
Develop test methods to measure volumetric flow rates in an environment simulating the human kidney
-
Understand the current solutions on the market through intellectual property (IP) and patents
-
Optimize and test laser settings to fracture and dust kidney stones under different conditions
-
Report findings in technical reports to senior engineers
Challenges:
-
Maneuvering uretroscopes proved to be challenging
-
Physicians undergo hours of clinical training to operate a uretroscope, and picking it up on the fly for testing is not easy
-
-
Lasering kidney stones in a controlled lab environment is difficult and takes a lot of training and practice
-
Similarly, operating high-intensity lasers and fragmenting kidney stones in a kidney-like environment is challenging
-
-
Communicating with senior engineers at times was difficult because we have very different depths of knowledge and experiences. Sometimes an answer would be clear to them and not to me.
Results:
-
Completed extensive testing comparing Boston Scientific's data to competitor data
-
Conducted in-depth volumetric flow rate testing to ensure patient safety and efficacy of our devices
-
Optimized laser settings for our specific ureteroscopy applications
-
Analyzed and processed raw empirical data
-
Developed mathematical models and formulae to draw conclusions and extrapolate data
-
Lessons Learned:
-
Efficacy in conducting tests
-
Due to the long and redundant nature of testing, I learned to be efficient in the lab
-
-
Clarity and preciseness in communicating critical data
-
Learned a lot about patents and IP by working with our lead engineer who has 300+ patents to his name
-
Familiarity with peristaltic pumps